The complex dangers of spoilage for life sciences organizations
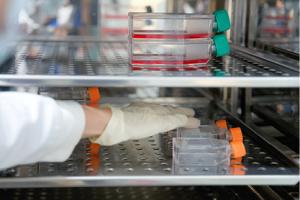
An article in our Plugged In tech and life sciences series
By Toni Mitchell, President of Technology and Life Sciences
Life sciences organizations handle materials and develop products in environments that are heavily regulated and climate controlled. This makes them uniquely vulnerable to costly and damaging claims in the event of spoilage and contamination. Agents can play a crucial role in helping these organizations navigate these risks and ensure their operations are properly prepared and protected.
Four key vulnerabilities
Being aware and knowledgeable about the unique considerations life sciences organizations face is key to providing risk management counsel and offering the right coverage solutions for your customers. Areas of risk related to spoilage for life sciences organizations include:
- Cold-chain vulnerability: Many life sciences products, such as pharmaceuticals and biologics, require strict temperature control to maintain efficacy and safety. Any change in temperature could result in these products being prohibited from distribution.
- Contamination prevention: Bacteria, viruses, or other pathogens can spoil products, especially in the production of biologics and other sensitive materials. Sterile environments and validated cleaning protocols are essential to prevent microbial contamination.
- Proper handling: Mishandling during transportation, storage, or within the production facility can lead to spoilage. This includes physical damage or exposure to unsuitable conditions. Incorrect labeling, improper storage, or failure to follow protocols can all result in spoilage.
- Regulatory compliance: Organizations must adhere to strict guidelines to ensure proper handling, storage, and transport. Failure to adhere to regulatory standards and guidelines results in the product being compromised and no longer viable for use.
Consequences of spoilage
The scope of a spoilage event can quickly exceed the impact to the product itself. Beyond financial loss due to wasted material, there are also costs associated with disposal, replacement of products, and often the need to reproduce the products. Spoilage can lead to operational disruptions, regulatory consequences and costly product recalls.
Consider this real example:
A widespread power outage that lasted for four days resulted in a life sciences company's refrigeration equipment inability to maintain the required temperature for their product. All of the impacted products had to be thrown out, resulting in a $370,000 claim. Add to that the potential for regulatory consequences from the FDA or a potential for product recalls, and the cost could continue to climb.
Not all solutions are created equal
It’s important to understand the potential impact of a spoilage event and the risk prevention and coverage options that can help ensure customers are well prepared. Not all coverage is created equal, and it's important that as agents consider coverage solutions for life sciences, unique aspects of their business are considered. For example, the spoilage coverage triggers in a standard policy may not extend coverage if a human error or mistake leads to a spoilage loss.
Providing advice for proactive prevention
Agents can add more value to life sciences organizations by helping them proactively mitigate these risks. By implementing robust quality control measures, investing in reliable storage and transportation systems, and ensuring compliance with regulatory standards, organizations will be well-positioned. In addition, continuous monitoring and staff training are essential to minimize the risk of spoilage. Agents can offer insight and guidance on a risk management program including:
- A 24-hour sensor system, like the Hanover i-on Sensor ProgramTM, to detect and monitor leaks and temperature changes
- Regular maintenance of refrigeration, cooling, or humidity control equipment
- Redundant refrigeration, cooling, or humidity control equipment
- Business continuity plans
Partnering with the right carrier
Even with the best controls in place, mistakes happen. But those mistakes can be costly to a life sciences organization if their carrier doesn’t provide the right protection.
That's why it's important to partner with a carrier that offers the industry knowledge, coverage, and risk management services needed to recover from spoilage and other potentially devastating threats. This includes coverage, such as all risk peril protection offered by The Hanover, that provides broader and more comprehensive safeguards created for life sciences businesses.
By understanding these risks and providing comprehensive coverage and support, agents can help life sciences organizations manage spoilage risks effectively.
Let's start a conversation today
Contact a member of our technology or life sciences teams to learn more about our coverage and services, and how we can help you tailor a solution for you and your clients.
Related resources
The complex dangers of spoilage for life sciences organizations
An article in our Plugged In tech and life sciences series
By Toni Mitchell, President of Technology and Life Sciences
Life sciences organizations handle materials and develop products in environments that are heavily regulated and climate controlled. This makes them uniquely vulnerable to costly and damaging claims in the event of spoilage and contamination. Agents can play a crucial role in helping these organizations navigate these risks and ensure their operations are properly prepared and protected.
Four key vulnerabilities
Being aware and knowledgeable about the unique considerations life sciences organizations face is key to providing risk management counsel and offering the right coverage solutions for your customers. Areas of risk related to spoilage for life sciences organizations include:
- Cold-chain vulnerability: Many life sciences products, such as pharmaceuticals and biologics, require strict temperature control to maintain efficacy and safety. Any change in temperature could result in these products being prohibited from distribution.
- Contamination prevention: Bacteria, viruses, or other pathogens can spoil products, especially in the production of biologics and other sensitive materials. Sterile environments and validated cleaning protocols are essential to prevent microbial contamination.
- Proper handling: Mishandling during transportation, storage, or within the production facility can lead to spoilage. This includes physical damage or exposure to unsuitable conditions. Incorrect labeling, improper storage, or failure to follow protocols can all result in spoilage.
- Regulatory compliance: Organizations must adhere to strict guidelines to ensure proper handling, storage, and transport. Failure to adhere to regulatory standards and guidelines results in the product being compromised and no longer viable for use.
Consequences of spoilage
The scope of a spoilage event can quickly exceed the impact to the product itself. Beyond financial loss due to wasted material, there are also costs associated with disposal, replacement of products, and often the need to reproduce the products. Spoilage can lead to operational disruptions, regulatory consequences and costly product recalls.
Consider this real example:
A widespread power outage that lasted for four days resulted in a life sciences company's refrigeration equipment inability to maintain the required temperature for their product. All of the impacted products had to be thrown out, resulting in a $370,000 claim. Add to that the potential for regulatory consequences from the FDA or a potential for product recalls, and the cost could continue to climb.
Not all solutions are created equal
It’s important to understand the potential impact of a spoilage event and the risk prevention and coverage options that can help ensure customers are well prepared. Not all coverage is created equal, and it's important that as agents consider coverage solutions for life sciences, unique aspects of their business are considered. For example, the spoilage coverage triggers in a standard policy may not extend coverage if a human error or mistake leads to a spoilage loss.
Providing advice for proactive prevention
Agents can add more value to life sciences organizations by helping them proactively mitigate these risks. By implementing robust quality control measures, investing in reliable storage and transportation systems, and ensuring compliance with regulatory standards, organizations will be well-positioned. In addition, continuous monitoring and staff training are essential to minimize the risk of spoilage. Agents can offer insight and guidance on a risk management program including:
- A 24-hour sensor system, like the Hanover i-on Sensor ProgramTM, to detect and monitor leaks and temperature changes
- Regular maintenance of refrigeration, cooling, or humidity control equipment
- Redundant refrigeration, cooling, or humidity control equipment
- Business continuity plans
Partnering with the right carrier
Even with the best controls in place, mistakes happen. But those mistakes can be costly to a life sciences organization if their carrier doesn’t provide the right protection.
That's why it's important to partner with a carrier that offers the industry knowledge, coverage, and risk management services needed to recover from spoilage and other potentially devastating threats. This includes coverage, such as all risk peril protection offered by The Hanover, that provides broader and more comprehensive safeguards created for life sciences businesses.
By understanding these risks and providing comprehensive coverage and support, agents can help life sciences organizations manage spoilage risks effectively.
Let's start a conversation today
Contact a member of our technology or life sciences teams to learn more about our coverage and services, and how we can help you tailor a solution for you and your clients.
Related resources
The complex dangers of spoilage for life sciences organizations
An article in our Plugged In tech and life sciences series
By Toni Mitchell, President of Technology and Life Sciences
Life sciences organizations handle materials and develop products in environments that are heavily regulated and climate controlled. This makes them uniquely vulnerable to costly and damaging claims in the event of spoilage and contamination. Agents can play a crucial role in helping these organizations navigate these risks and ensure their operations are properly prepared and protected.
Four key vulnerabilities
Being aware and knowledgeable about the unique considerations life sciences organizations face is key to providing risk management counsel and offering the right coverage solutions for your customers. Areas of risk related to spoilage for life sciences organizations include:
- Cold-chain vulnerability: Many life sciences products, such as pharmaceuticals and biologics, require strict temperature control to maintain efficacy and safety. Any change in temperature could result in these products being prohibited from distribution.
- Contamination prevention: Bacteria, viruses, or other pathogens can spoil products, especially in the production of biologics and other sensitive materials. Sterile environments and validated cleaning protocols are essential to prevent microbial contamination.
- Proper handling: Mishandling during transportation, storage, or within the production facility can lead to spoilage. This includes physical damage or exposure to unsuitable conditions. Incorrect labeling, improper storage, or failure to follow protocols can all result in spoilage.
- Regulatory compliance: Organizations must adhere to strict guidelines to ensure proper handling, storage, and transport. Failure to adhere to regulatory standards and guidelines results in the product being compromised and no longer viable for use.
Consequences of spoilage
The scope of a spoilage event can quickly exceed the impact to the product itself. Beyond financial loss due to wasted material, there are also costs associated with disposal, replacement of products, and often the need to reproduce the products. Spoilage can lead to operational disruptions, regulatory consequences and costly product recalls.
Consider this real example:
A widespread power outage that lasted for four days resulted in a life sciences company's refrigeration equipment inability to maintain the required temperature for their product. All of the impacted products had to be thrown out, resulting in a $370,000 claim. Add to that the potential for regulatory consequences from the FDA or a potential for product recalls, and the cost could continue to climb.
Not all solutions are created equal
It’s important to understand the potential impact of a spoilage event and the risk prevention and coverage options that can help ensure customers are well prepared. Not all coverage is created equal, and it's important that as agents consider coverage solutions for life sciences, unique aspects of their business are considered. For example, the spoilage coverage triggers in a standard policy may not extend coverage if a human error or mistake leads to a spoilage loss.
Providing advice for proactive prevention
Agents can add more value to life sciences organizations by helping them proactively mitigate these risks. By implementing robust quality control measures, investing in reliable storage and transportation systems, and ensuring compliance with regulatory standards, organizations will be well-positioned. In addition, continuous monitoring and staff training are essential to minimize the risk of spoilage. Agents can offer insight and guidance on a risk management program including:
- A 24-hour sensor system, like the Hanover i-on Sensor ProgramTM, to detect and monitor leaks and temperature changes
- Regular maintenance of refrigeration, cooling, or humidity control equipment
- Redundant refrigeration, cooling, or humidity control equipment
- Business continuity plans
Partnering with the right carrier
Even with the best controls in place, mistakes happen. But those mistakes can be costly to a life sciences organization if their carrier doesn’t provide the right protection.
That's why it's important to partner with a carrier that offers the industry knowledge, coverage, and risk management services needed to recover from spoilage and other potentially devastating threats. This includes coverage, such as all risk peril protection offered by The Hanover, that provides broader and more comprehensive safeguards created for life sciences businesses.
By understanding these risks and providing comprehensive coverage and support, agents can help life sciences organizations manage spoilage risks effectively.
Let's start a conversation today
Contact a member of our technology or life sciences teams to learn more about our coverage and services, and how we can help you tailor a solution for you and your clients.
Related resources
The complex dangers of spoilage for life sciences organizations
An article in our Plugged In tech and life sciences series
By Toni Mitchell, President of Technology and Life Sciences
Life sciences organizations handle materials and develop products in environments that are heavily regulated and climate controlled. This makes them uniquely vulnerable to costly and damaging claims in the event of spoilage and contamination. Agents can play a crucial role in helping these organizations navigate these risks and ensure their operations are properly prepared and protected.
Four key vulnerabilities
Being aware and knowledgeable about the unique considerations life sciences organizations face is key to providing risk management counsel and offering the right coverage solutions for your customers. Areas of risk related to spoilage for life sciences organizations include:
- Cold-chain vulnerability: Many life sciences products, such as pharmaceuticals and biologics, require strict temperature control to maintain efficacy and safety. Any change in temperature could result in these products being prohibited from distribution.
- Contamination prevention: Bacteria, viruses, or other pathogens can spoil products, especially in the production of biologics and other sensitive materials. Sterile environments and validated cleaning protocols are essential to prevent microbial contamination.
- Proper handling: Mishandling during transportation, storage, or within the production facility can lead to spoilage. This includes physical damage or exposure to unsuitable conditions. Incorrect labeling, improper storage, or failure to follow protocols can all result in spoilage.
- Regulatory compliance: Organizations must adhere to strict guidelines to ensure proper handling, storage, and transport. Failure to adhere to regulatory standards and guidelines results in the product being compromised and no longer viable for use.
Consequences of spoilage
The scope of a spoilage event can quickly exceed the impact to the product itself. Beyond financial loss due to wasted material, there are also costs associated with disposal, replacement of products, and often the need to reproduce the products. Spoilage can lead to operational disruptions, regulatory consequences and costly product recalls.
Consider this real example:
A widespread power outage that lasted for four days resulted in a life sciences company's refrigeration equipment inability to maintain the required temperature for their product. All of the impacted products had to be thrown out, resulting in a $370,000 claim. Add to that the potential for regulatory consequences from the FDA or a potential for product recalls, and the cost could continue to climb.
Not all solutions are created equal
It’s important to understand the potential impact of a spoilage event and the risk prevention and coverage options that can help ensure customers are well prepared. Not all coverage is created equal, and it's important that as agents consider coverage solutions for life sciences, unique aspects of their business are considered. For example, the spoilage coverage triggers in a standard policy may not extend coverage if a human error or mistake leads to a spoilage loss.
Providing advice for proactive prevention
Agents can add more value to life sciences organizations by helping them proactively mitigate these risks. By implementing robust quality control measures, investing in reliable storage and transportation systems, and ensuring compliance with regulatory standards, organizations will be well-positioned. In addition, continuous monitoring and staff training are essential to minimize the risk of spoilage. Agents can offer insight and guidance on a risk management program including:
- A 24-hour sensor system, like the Hanover i-on Sensor ProgramTM, to detect and monitor leaks and temperature changes
- Regular maintenance of refrigeration, cooling, or humidity control equipment
- Redundant refrigeration, cooling, or humidity control equipment
- Business continuity plans
Partnering with the right carrier
Even with the best controls in place, mistakes happen. But those mistakes can be costly to a life sciences organization if their carrier doesn’t provide the right protection.
That's why it's important to partner with a carrier that offers the industry knowledge, coverage, and risk management services needed to recover from spoilage and other potentially devastating threats. This includes coverage, such as all risk peril protection offered by The Hanover, that provides broader and more comprehensive safeguards created for life sciences businesses.
By understanding these risks and providing comprehensive coverage and support, agents can help life sciences organizations manage spoilage risks effectively.
Let's start a conversation today
Contact a member of our technology or life sciences teams to learn more about our coverage and services, and how we can help you tailor a solution for you and your clients.